Technology
With a primary focus in bitumen modification and specialized manufacturing, RAETEX maintains a strong commitment to product quality and performance. To achieve this, RAETEX puts stringent quality control and robust research and development at the forefront of its activities. This ensures reproducibility and reliability of material test results and ultimately, consistent quality in the final product. When combined with continued engagement and on-going technical support, the consistency and reliability of its modified binders allows RAETEX to be seen as a trusted partner in the pavement and construction industry.
- Sustainable and environmentally-friendly through energy savings and a reduction in VOCs, CO2, SO2, and NOx emissions during asphalt production and construction;
- Improved performance over time resulting in life cycle cost benefits;
- Enhanced moisture resistance and aggregate packing during compaction through improved adhesion.
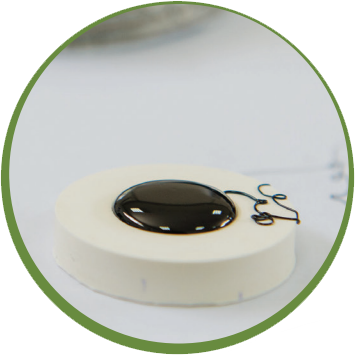
- Sustainable and environmentally-friendly through the reduction of post-consumer waste materials that are harmful to dispose of and dangerous to store;
- Improved pavement safety: increases skid resistance due to rubber on rubber traction and decreases spray in wet conditions;
- Noise reduction of pavement by 2-4 dBa;
- Protection against Urban Heat Island effect.